Kaizen (改善) is a Japanese word that has two components – Kai 改(Change) and Zen 善 (Good) which translates to “Good Change”, “Change for the Better” or “Continuous Improvement.” It involves making changes for the better, small incremental changes that eventually amounts to extraordinary progress and result. In a business context, Kaizen refers to activities that continuously improve all functions and it usually involves everyone in the organizational value-chain from the CEO to the assembly line workers.
Kaizen was first implemented in Japanese factories and businesses after World War II. It was greatly influenced by American business and quality-management consultants like W. Edwards Deming who worked with Japanese industry leaders after world war II. It is one of the guiding principles of the Toyota Way. Other prominent Kaizen pioneers include Shigeo Shingo (Toyota Production System) and Masaaki Imai (Founder of Kaizen Institute).
The Toyota Way is a set of principles and behaviors that underlie the Toyota Motor Corporation’s managerial approach and production system. In 2001, the Toyota Corporation published some set of guidelines and principles to clarify its values and business methods. The document was called “Toyota Way 2001“. It consists of two main pillars: “Continuous Improvement” and “Respect for People”. The Toyota Way further sub-divided continuous improvement into 3 sub-pillars: Challenge, Kaizen and Genchi Genbutsu (現地現物) which translates to “go and See”.
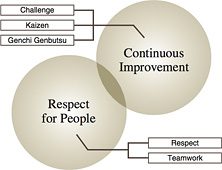
Kaizen is mostly associated with manufacturing processes such as the one popularised in the Toyota Production System Originally called “just-in-time production” and it has also been used in other non-manufacturing environments/industries such as Healthcare, Information Technology, PsychoTherapy, Government, Banking, Supply Chain Management, etc.